Database
Contact Information in China
Germany Fala Cofer (Group) Co., Ltd
Address:Room C1D, 6/F, Wing Hing Industrial Building, No.14 Hing Yip Street, Kwun Tong, Kowloon, Hong Kong
Telephone:00852-96669759
Fax:00852-21100996
Address:Room C1D, 6/F, Wing Hing Industrial Building, No.14 Hing Yip Street, Kwun Tong, Kowloon, Hong Kong
Telephone:00852-96669759
Fax:00852-21100996
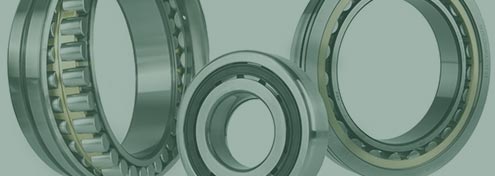
Reason and restoring of running outer ring for crankshaft fore bearings
The outer ring rotates in bearing bore often occurred when engine crankshaft fore bearing operating, also known as running outer ring for bearing. Running outer ring can make bearing bore quickly larger, misalignment will also increased for the fore & rear bearing bore of crankshaft, thus to make crankshaft broken and cause cracks for cylinder block. At the same time, bearing roller was tightly pressed into the housing ring, so the roller protector may be damaged or cause flaking for the surface of roller, bearing life also reduced when operating.
Bearing outer ring and bearing bore use over-transition fit, which can easily lead to running outer ring for bearing, mainly due to:
1. Excessive vibration generated during engine operating;
2. Explosion pressure generated when engine operating, among which parts of force passed to the block through the connecting rod, crankshaft and bearing. As a result, bearing’s outer ring can rotate during this proces;
3. Temperature effect. Generally speaking, the temperature for bearing’s inner ring is 10 ℃ higher than the outer ring, the clearance between roller and raceway may disappear due to the different thermal expansion, even to cause interference fit. Consequently, the roller protector will be squeezed, or the outer ring may rotate.
When crankshaft fore bearing running outer ring, take following measures to restore:
1. Strictly controll the misalignment of bearing bore, misalignment of the main journal for crankshaft and the non-parallelism between the centerline of connecting rod & the main journal when repairs.
2. After bearing running outer ring, it can plate Babbitt alloy at the surface of the outer ring, which is much better. The detailed method is: removing the oil on the surface of the bearing’s outer ring (no need to dismount bearing from the crankshaft); burning Babbitt alloy with hot iron, then evenly coating on the surface of the outer ring, or melting Babbitt alloy in the container, making bearing revolve in the melting solution. But be careful not to stick the alloy to the roller; folding the crankshaft with bearing on vise, and dressing the outer ring to the required size with flat file.
3. Clamping cooper or cutting groove to hit the pin between bearing and bearing bore. And the way for clamping cooper is just temporary, as it can not dress ellipticity, and make the bearing bore’s misalignment increased, thus the effect is not so good. Or cutting groove to hit the pin on bearing bore and seat ring, which will spoil bearing and cylinder due to the stress concentration caused in the cutting groove.
Bearing outer ring and bearing bore use over-transition fit, which can easily lead to running outer ring for bearing, mainly due to:
1. Excessive vibration generated during engine operating;
2. Explosion pressure generated when engine operating, among which parts of force passed to the block through the connecting rod, crankshaft and bearing. As a result, bearing’s outer ring can rotate during this proces;
3. Temperature effect. Generally speaking, the temperature for bearing’s inner ring is 10 ℃ higher than the outer ring, the clearance between roller and raceway may disappear due to the different thermal expansion, even to cause interference fit. Consequently, the roller protector will be squeezed, or the outer ring may rotate.
When crankshaft fore bearing running outer ring, take following measures to restore:
1. Strictly controll the misalignment of bearing bore, misalignment of the main journal for crankshaft and the non-parallelism between the centerline of connecting rod & the main journal when repairs.
2. After bearing running outer ring, it can plate Babbitt alloy at the surface of the outer ring, which is much better. The detailed method is: removing the oil on the surface of the bearing’s outer ring (no need to dismount bearing from the crankshaft); burning Babbitt alloy with hot iron, then evenly coating on the surface of the outer ring, or melting Babbitt alloy in the container, making bearing revolve in the melting solution. But be careful not to stick the alloy to the roller; folding the crankshaft with bearing on vise, and dressing the outer ring to the required size with flat file.
3. Clamping cooper or cutting groove to hit the pin between bearing and bearing bore. And the way for clamping cooper is just temporary, as it can not dress ellipticity, and make the bearing bore’s misalignment increased, thus the effect is not so good. Or cutting groove to hit the pin on bearing bore and seat ring, which will spoil bearing and cylinder due to the stress concentration caused in the cutting groove.
Knowledge/ArticleMore
- Questions & answers for bearing lubricat
- Design and fix of bearings for crank arm
- Turning method for repair of camshaft be
- Structure improvement on inactive self-l
- Brief analysis on assembly points of pre
- Reason and restoring of running outer ri
- New method for bearing assembly heating
- Maintenance for wheel bearing of cars (d